Building a Lightbox
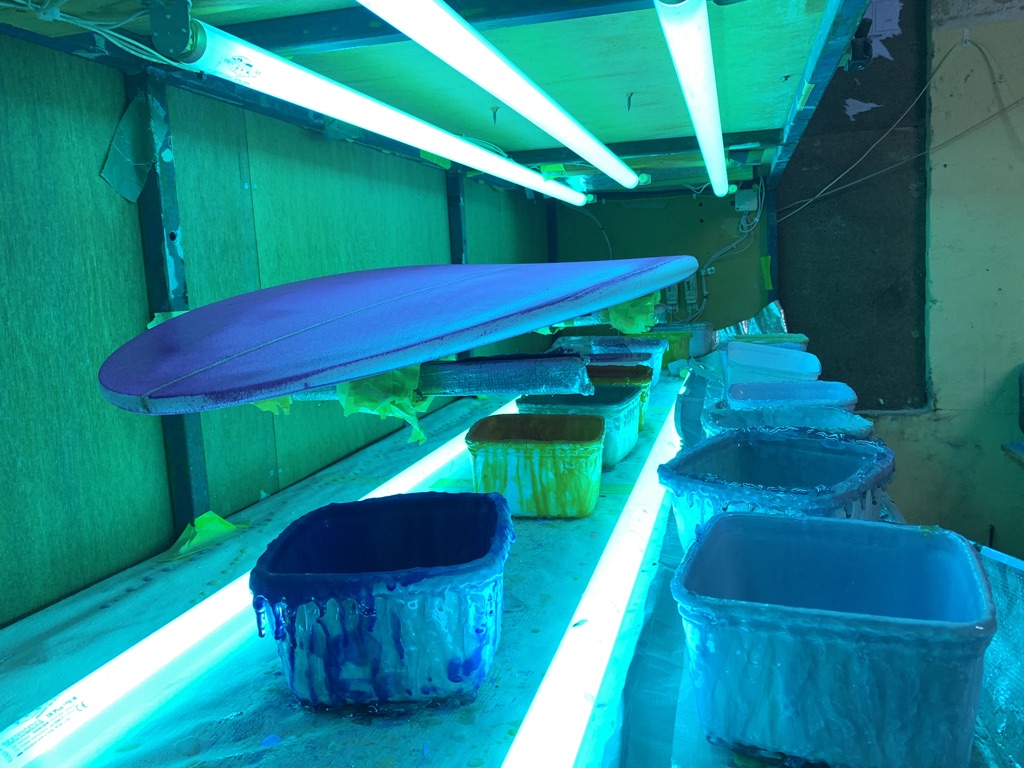
To ensure consistency and quality in your glassing factory environment, it is best to use a Lightbox. Here are some useful tips and hints on building and installing a Lightbox in your factory:
- What do I need to construct a Lightbox?
- What are the best lights to use?
- Important points when building your Lightbox
If you need any additional help or would like to ask some more questions, please contact us directly.
What do I need to construct a Lightbox?
This depends on what sort of Lightbox you want to build. Some glassers prefer to have a stationary box either on a stand or attached to the wall. Others build a box on wheels so that it can be moved around the factory floor. You should note that a movable box will require large turning circles (to manoeuvre over the board and stand) and may not be suited to smaller factories. A stationary box will require you to physically transport the board to and from the box.
In each case you will need either steel, aluminium or wood to construct the frame and a set of good UV emitting light sources. Soltek recommends the use of UV tubes (as detailed in the next question). We recommend you get a qualified electrician to wire up the lights properly. If using metal to construct the frame you will need to weld the joints to ensure strength. Soltek also recommends you close the Lightbox to ensure all UV light is contained within the board curing area. Prolonged exposure to UV may be harmful and having UV light being emitted into the factory while glassing may promote premature curing.
What are the best lights to use?
There is a wide variety of artificial UV lighting. You are predominantly interested in lights that emit UV-A. There are two types of lighting which can be used to cure resin catalysed with UV Catalyst+. The first is bulb-based and includes Mercury Vapour and Metal Halide lamps. These are not suitable for building a Lightbox since they generate too much heat and do not provide an even and broad UV light emission. The second type, is tube-based and is ideal for Lightbox applications. Tube lights such as UV Tanning tubes and black lights, provide an even and consistent light without generating excess heat.
UV tubes, come in a variety of lengths and power outputs depending on where they are sourced from. General lighting suppliers carry a limited range whereas specialist suppliers (who deal solely in the sale of UV lighting) offer lengths including 5ft and 6ft, and power outputs starting from 40W to several 100W. Note the higher the power output the higher the heat generation.
What points do I need to remember when making my box?
There are a number of things to consider when building a Lightbox. First you need to decide whether you are going to make a stationary box or one that is capable of being moved over the board. Then you need to determine how many tubes you will require. The number needed depends first on the way you configure them within the box and then on the length of your box. If building a stationary box you can make it long enough to cure both longboards and shortboards. In each case you need to ensure that once the board is in the box it is given an even coverage of light.
Most Lightboxes fail because the builder has unintentionally created shadows. This typically occurs in the rail and lap region, where there is a discontinuity in the light or an object (commonly the board stand) prevents light from reaching the resin. Thus always ensure continuity in light by placing tubes end-to-end or having an overlap. Also, ensure the board stand is supported from the bottom of the box not the side. This will create consistent lighting around the board and in the critical rail and lap regions. Soltek recommends placing lights just under the rails (to promote cure of rails and laps) and then evenly spacing lighting over the rest of the board. Note, you do not need any lights directly under the board since you cure each side of the board in two separate steps, hence always placing the side which needs curing upward.
The length of a movable Lightbox should be kept to a shortboard size as a maximum. Otherwise the box becomes too big and cumbersome. Some glassers have managed to create innovative designs which allow multiple boards to cure in a stacking configuration. Others use reflective material (such as foils) to increase reflection within the box and promote faster curing. You have complete flexibility in designing your box to meet the needs of your factory and annual volumes. Just remember, use the right lights and have them configured correctly, and you will have no problems.